Kraków 2024-12-22
Passenger wagons type 111A of UIC-Y standard.
The 111A type wagons are 2nd class cars with 10 compartments, each with eight seats. The car was designed in 1969, but work on it had been going on since 1963.
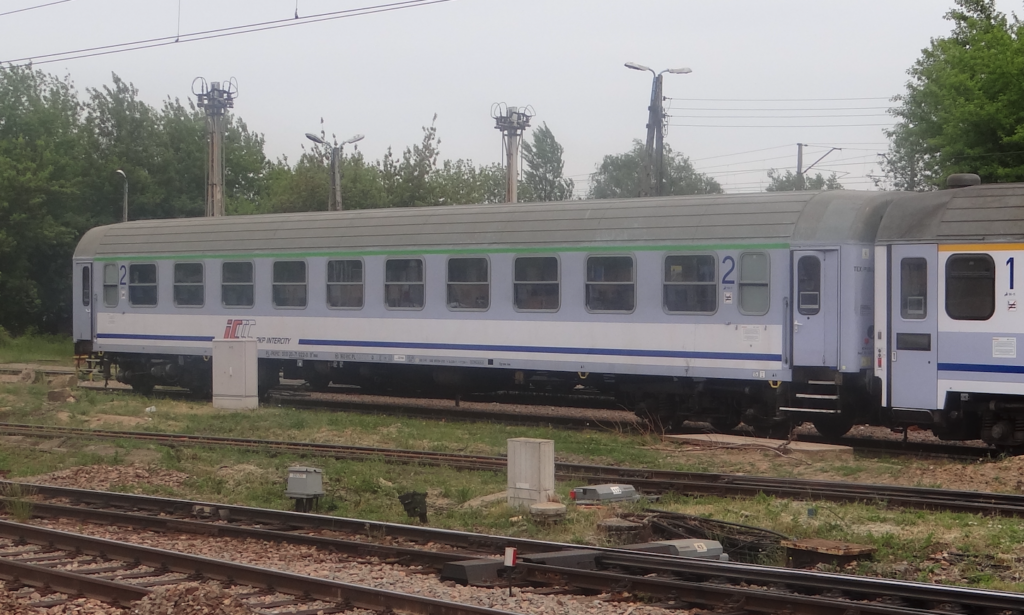
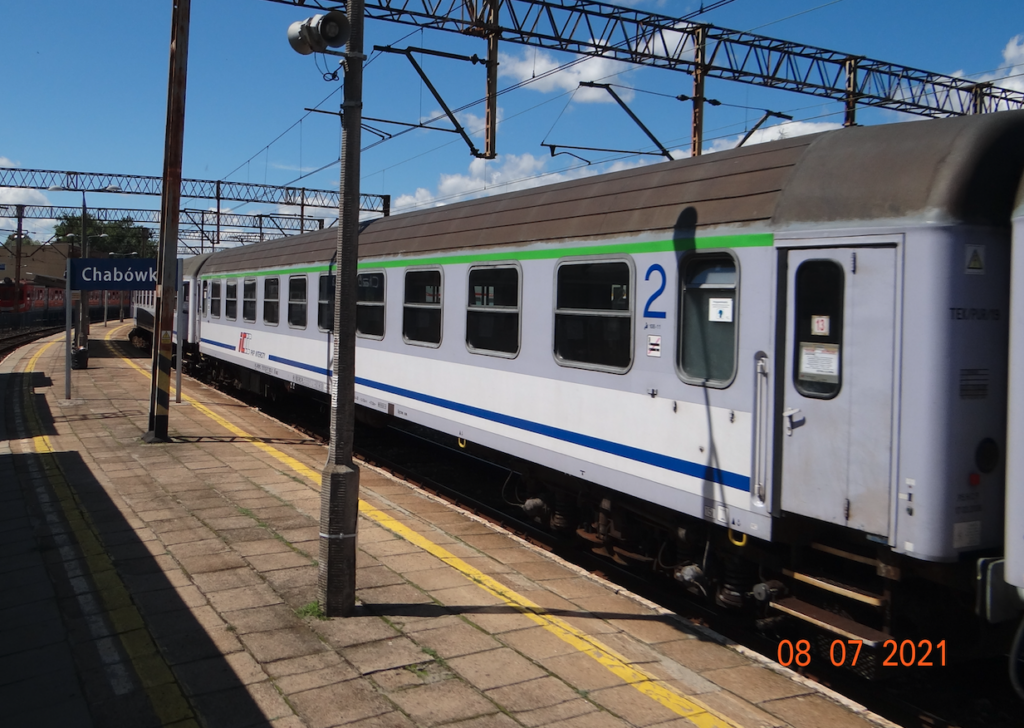
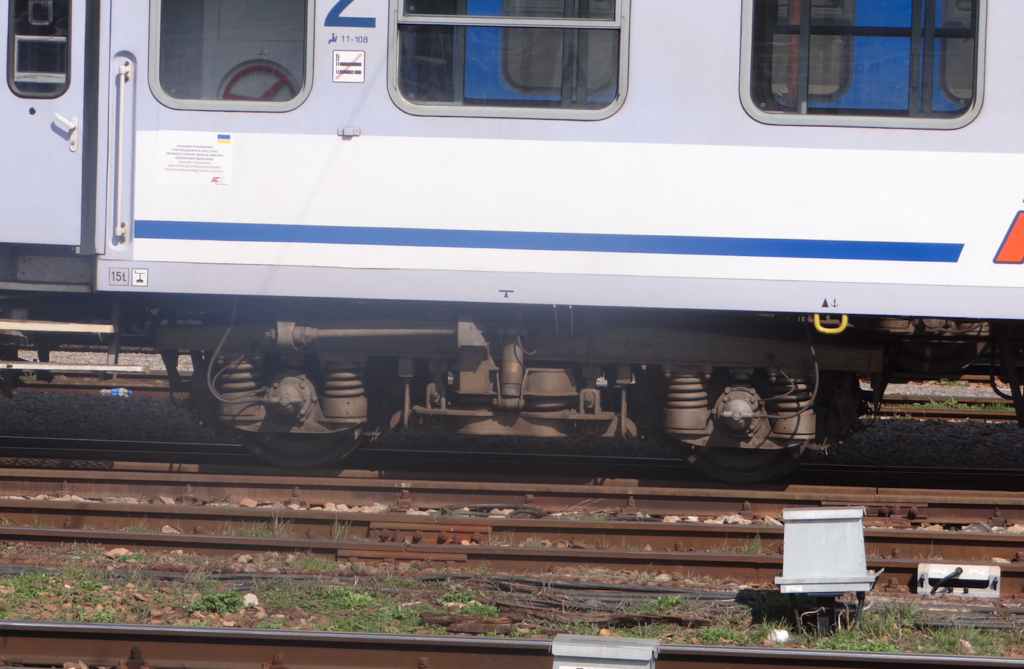
History
Initial operation of the 104A type wagons was very difficult. A large number of the 104A type wagons suffered from failures of various components. There were cases of the heater’s thermal protection being triggered at the wrong time, water installations freezing, and damage to the power supply and lighting converters. The communist authorities are to blame for this situation. In the conditions of a centralized economy and chronic lack of foreign exchange, all matters had to be kept open until the contract was concluded. In practice, designers had to pre-select devices, but this could not be communicated to bidders until the contract was concluded. In communist Poland, not many modern devices were manufactured, and they were not even manufactured in the entire communist kolkhoz. A classic example is air conditioning for passenger cars, which in the 1960s, in Western Europe, was already a standard.
The problem with the 104A type wagons, and especially the 104Ac type, was that its version designated type 66W was manufactured for the needs of the CCCP. Since there were failures that could not be repaired at ZNTK, these wagons in freight trains returned to Poznań to HCP. The matter was so serious that party elements took up the matter and ordered the Supreme Audit Office to investigate the matter. An immediate investigation was launched and people in contact with foreigners (companies from Western Europe) were questioned in order to detect possible abuses. The accusation was absurd; Why were prototype components used in the 104Ac type wagon? The HCP plant responded that either we would use new, modern Polish solutions or we would import them for foreign currency. As a result, the Supreme Audit Office itself sided with the engineers from HCP. The aftermath of this matter was the issuing of a communist ordinance; On improving the quality of passenger wagons and trams. In communist conditions, such ordinances had minimal significance, as they only meant an intensification of the paper war between the interested parties. This order was more to show the Muscovites that the PZPR was active and vigilant.
The 104Ac type car was to be a modern car meeting UIC-Y standards, with a maximum speed of 160 km/h.
In 1963, in parallel with the 104Ac type car, a design for the 104Aa type car was created. This car was designed without a modern electrical system, based on domestic, already produced components. It was equipped with a domestic air heating system, with the import of magnetic valves and pressure switches for the steam heating system limited to a minimum. The heating concept was developed by the Institute of Thermal Technology (ITC) in Łódź in cooperation with CBK PTK in Poznań.
It took several years to perfect the passenger car based on the 104Ac type car, which was eventually designated type 111A and type 112A. Both cars have a total length of 24.50 m. The 111A type car is a 2nd class car with 10 compartments and 8 seats in each compartment. The 112A type car is a 1st class car with 9 compartments and 6 seats in each compartment.
In 1969, an improved 2nd class passenger car was designed. It received the designation type 111A. In the literature, the manufacturer’s mark HCP or PaFaWag is often added. The 111A type car, depending on the bogies used, is designed for a speed of 140 or 160 km/h. The cars were produced (with breaks) from 1969 to 1992. In HCP, 2nd class passenger cars of the 111A type were built in the period 1969-1971 and 1977-1978. They were produced at the PaFaWag plant in the period 1969-1992. Some sources indicate that production started in 1967. A total of 2,825 units were produced (other sources indicate 2,323 units), making the type 111A the longest series of wagons in Poland. Currently (2021) there are about 1,500 wagons in use, and many of them have undergone numerous modifications.
Approximately 2,323 111A/112A type wagons were produced in the following versions:
Type 111A wagon (215 units) produced in the period 1967-1971.
Type 111Ab wagons (213 units) produced in the period 1971-1972.
Type 111Ac wagons (301 units) produced in the period 1973-1975.
Type 111Ad wagons, equipped with steam and electric resistance heating.
Type 111Af wagons, equipped with two-channel air heating, intended for the Odra Wrocław – Warsaw express.
Type 111Ag wagons, equipped with steam and electric (resistance) heating.
111Ah type wagons (538 units) manufactured in the period 1979-1986.
111Ak type wagon manufactured in 1979, mounted on GP200 type bogies.
111Al type wagon manufactured in 1983, mounted on 11AN type bogies.
111Am type wagon.
111Ao type wagon.
111Ap type wagons (236 units) manufactured in the period 1982-1985 and 1989, equipped with steam and electric (resistance) heating.
111Ap-N type wagon, prototype with a disabled compartment.
Type 111Ar wagons (10 units) manufactured in 1985-1986, equipped with different bogies, type 4ANhe-6.
Type 111As wagons (196 units) manufactured in 1983-1985, equipped with steam and electric (resistance) heating.
Type 111At wagons (3 units) manufactured in 1985-1986, equipped with 4ANhe-6 bogies.
Type 111Au wagons (125 units) manufactured in 1984-1986, without steam heating, only electric.
Type 111Aw wagons (360 units) manufactured in 1986-1988, have electric blowing heating.
Type 111Ax cars (30 units) manufactured in 1989, have steam and electric air heating.
Type 111Ay cars (90 units) manufactured in 1988-1989, have electric air heating.
Type 112A cars are 1st class cars, with 9 compartments, each with 6 seats. The seats are adjustable and extendable. Production of cars;
Type 112Ad cars, 64 units, built in 1967-1968.
Type 112Af cars, 66 units, manufactured in 1968-1969.
Type 112Ag cars, 669 units, manufactured in 1978-1984.
Type 112Ah wagons, 15 units, manufactured in 1980-1985.
Type 112Aj wagons, 1985.
Type 112Ak wagons, 1985.
Type 112Am wagons, manufactured in 1986-1987.
Type 112Ap wagons, 1989.
Type 112Ar wagons, manufactured in 1988-1989.
Type 140A wagons, 60 units, manufactured in 1990-1991, forced air heating.
Construction of 111A type wagons.
In relation to heating and lighting, UIC regulations did not impose detailed solutions, only requirements that wagons should meet. UIC regulations required that the battery capacity should be sufficient for 5 hours of full lighting operation and 3 hours for lighting and heating. A 5-hour power supply for both receivers was already recommended at that time. The problem was that in the 1960s, at each border, Polish wagons stood for several hours because of detailed customs control. This fact kept engineers awake at night. Therefore, the heating and electrical installation had to be well-designed and reliable. With a minimal foreign exchange input.
Engineers received a lot of help from companies in the UK and Italy. Solutions observed abroad helped develop Polish equivalents. Acid batteries were manufactured by the Battery Factory in Bielsko-Biała, which offered modern 500 Ah, large-area WP type acid batteries. The Western European market was interested in these batteries. The generator was a bigger problem. The PW 110 generator with a belt drive, with a power of 2.1 kW, 30 V, was already outdated and inefficient. However, at that time, domestic 4.5 kW, 30 V DC generators had already appeared in Poland, which met the requirements.
Polish engineers devoted a lot of attention to the electrical installation. Lighting was introduced for entrance steps, mirrors in toilets and inter-car passages. Light signals indicating the occupancy of toilets were also introduced. An isolated internal 220 V, 50 Hz network was introduced to power mechanical devices, such as vacuum cleaners (for cleaning crews), shavers, hair dryers (for travelers). A 24 V DC/220 V 50 Hz AC converter was used for this. Shaving sockets with automatic switching on of a special shaving converter were protected by a patent.
The lighting level in the compartments was to be at least 80 Lx. Unlike foreign designs, two 40 W fluorescent lamps were used instead of one, which guaranteed very good general lighting. Work was also carried out on an electric inter-car connector for the audio system (transmitting railway information). It was possible to individually adjust the volume in the compartments. Work was carried out on the possibility of broadcasting entertainment programmes, such as music, in all the cars of the train. In its final form, it was to be a kind of radio centre.
Initially, the cars were equipped only with steam heating. Later, when the rolling stock industry got involved in the production of the 43A type car and derivatives, PKP experienced a need for long-distance compartment cars additionally equipped with 3 kV electric heating.
Due to the specific situation in Poland, i.e. a large number of steam locomotives and the simultaneous electrification of the routes, it was decided that the cars should have steam and electric heating. This was not due to Poland’s backwardness, but to economic calculations. Crude oil had to be imported, and we had and still have hard coal locally. Long electric heaters with a voltage of 1500 V (3 kV insulation) were used in the wagons. They met the UIC standard requirements for heating in international traffic.
An important issue was the wide use of aluminum alloys in the production of passenger wagons. At that time, the demand for aluminum alloys in the aviation industry dropped significantly, because the production of combat aircraft decreased. On the other hand, the aluminum smelter in Skawina was working at full capacity. The railway industry and travelers took advantage of this situation, receiving elegant wagons. Several methods of passivation of aluminum alloys were developed and used in the production of windows and doors in wagons.
In the 1960s, laminates were widely introduced to the construction of passenger wagons. Polish plants had already mastered their production, and the quality was very high. Laminates are key in the railway industry, where they are used to produce wagon elements and track infrastructure. Their resistance to corrosion, high temperature and chemicals makes them suitable for harsh environments. They are used for housing electrical devices, cable covers, chassis elements and interior finishing of railcars. The lightness of these materials allows for a reduction in the weight of vehicles, which reduces energy consumption and maintenance costs.
External appearance of a 111A type wagon.
Externally, the 111A type wagons are distinguished by the number of windows: 10 full-size and 2 smaller ones in the toilets/vestibules. The toilet windows have frosted glass. There are also windows in the entrance doors. The roof can be grooved or smooth (PaFaWag). There can be a different number of vents on the roof of the wagon and their arrangement. The wagons differ in the handrails for boarding. The entrance to the wagon has three or two steps. The entrance doors are folding, much more convenient to open than single-leaf doors, although they are still opened manually. The lower edge of the body has a rolled-up edge (PaFaWag) or straight (HCP). In some types of wagons, rolling bogies other than 4ANc were used.
The wagons were heated by steam and electricity. Since 1973, production of wagons (111Ac) equipped only with electric heating was started. In the 80s, electric heating was already installed – forced air heating. In 1984, the production of wagons with alternative steam heating was completely abandoned. Steam heating was used when the train was in steam or diesel traction (locomotives SP42, SU45, SU46).
All wagons in Poland were painted dark green (olive). Class 1 wagons had an additional gold (yellow) stripe above the windows. Roofs were painted grey, and bogies were black. In the central place on the side of the wagon, the PKP inscription was placed, and under it the digital designation of the wagon. Near the entrance door, there was a number of the wagon class and possibly the information “Non-smoking wagon”, “Smoking wagon”.
Construction of the 111A wagon.
The wagon body is made of low-alloy carbon steel. The frame, side walls, front walls and roof are welded and welded, creating a uniform self-supporting structure. The frame is made of bent C-sections from 3 mm thick sheet metal. The wagon skeleton is made of bent sections 2-3 mm thick. The body cover is made of 2 mm thick sheet metal. For the grooved roof, 1 mm thick sheet metal is used. Thermal and acoustic insulation is installed in the frame. The moisture and corrosion insulation is made of asphalt paints, with a coating thickness of about 1-2 mm. Additionally, polystyrene boards are used. The front walls of the wagon have rounded edges, for a more streamlined shape.
Full-size windows are made of aluminum alloys, divided into two parts; the lower part is fixed, the upper part opens downwards. The windows have double glazing, 5 mm thick. In the 80s, some windows were installed as a single double glazing, not opening. The windows in the vestibules and toilets are smaller with a hinged upper part. The toilets have frosted glass. The internal windows are made of single 5 mm thick glass.
Pine or spruce beams are placed on the base, and on them impregnated plywood with a thickness of 15, 17 or 19 mm. Vinyl is placed on the plywood, which is welded at the joints. The floor in the toilets is made as a bathtub made of polyester or epoxy resin, reinforced with glass fibre. The partition walls are made of waterproof plywood with a thickness of 8-10 mm. Felt and polystyrene are used for soundproofing and insulation. Laminate and aluminium or plastic profiles are used as finishing.
The gangways between the cars have double-leaf doors mounted, which are manually pushed to the sides. From the outside, the doors between the cars are covered with rubber rollers. The cars have a classic screw coupling and classic buffers equipped with springs. The buffer stroke is 11 cm. Each end of the car is equipped with two electric red lights, and additionally hooks for end-of-train signals. The front wall contains high-voltage electrical connectors, brake installation and steam heating installation.
Interior finish.
The carriage has soft couches in the compartments. Four passengers could fit on one couch. The couches had armrests on the edges and in the middle. Fabric upholstery. Initially brown with patterns with the PKP logo. Above the couches were shelves for hand luggage and suitcases. Seat numbers were placed above the seats. The windows were fitted with curtains made of brown-beige fabric with the PKP logo. The walls were lined with boards made of hard decorative laminate of the Unilam type, in the colour of wood. The doors to the compartment were pushed aside manually. The corridor was lined with decorative laminate of the Unilam type. Folding seats between the windows. The carriage was lit with lamps equipped with fluorescent lamps. Hard linoleum (vinileum) 3-5 mm thick was laid on the floor. The vinyl is welded at the joints. The corridor is separated from the vestibules by swinging doors. Between the compartments and the corridor there are light walls made of waterproof plywood and 5 mm thick glass. The interior finish is dominated by aluminium alloys, in silver or gold. The strips cover the joints of the laminated panels and protect sharp edges.
Rolling bogies.
The wagons were fitted with 4AN type bogies. The two-axle bogie and with the service weight of the wagon 39,500 kg, it worked well. Travelling speeds of up to 160 km/h were not a problem and the running was smooth. Initially, the Oerlikon type braking system was used. The brakes are block type. Emergency brake levers were placed in the corridor inside the wagons and in each of the compartments. Cables ran from the emergency brake handle to the Ackerman flap, the opening of which caused the air pressure in the main pipe to drop and the train to stop. Each wagon was also equipped with a manual screw brake, activated from one of the vestibules using a wheel with a crank installed there. Over time, modernized 4ANc type bogies were installed. 4ANc type bogies were installed in some wagons even until 1992. There are also 4ANh, 4ANg bogie versions.
Written by Karol Placha Hetman