Piła 16-08-2024
Hybrid Traction Unit (HZT).
The Impuls 2 Hybrid Traction Unit type EN63H-009 is the first Polish train that, in addition to an electric drive powered by a 3 kV DC traction network, also has a diesel drive, in the form of the MTU PowerPack system. This system allows the train to move on routes without electric traction.
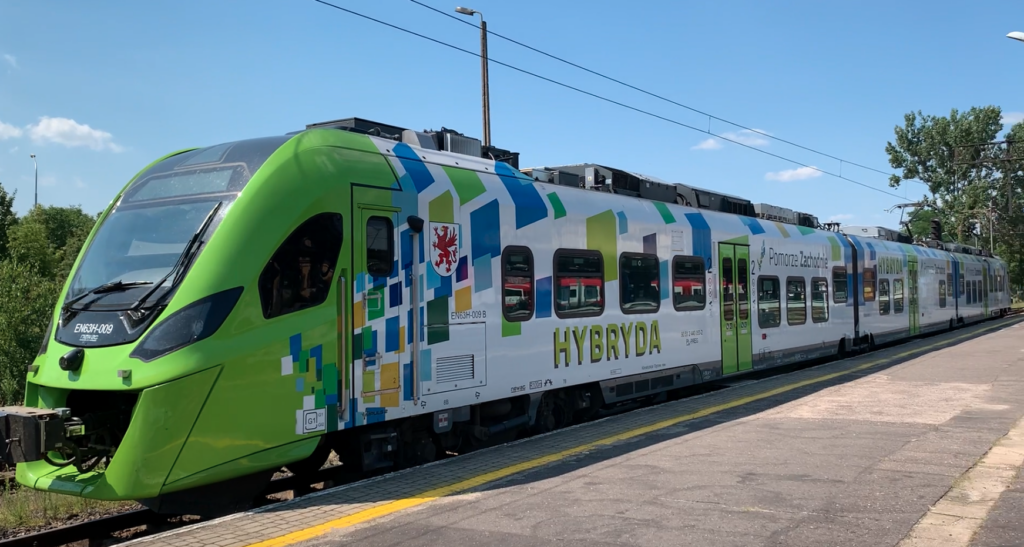
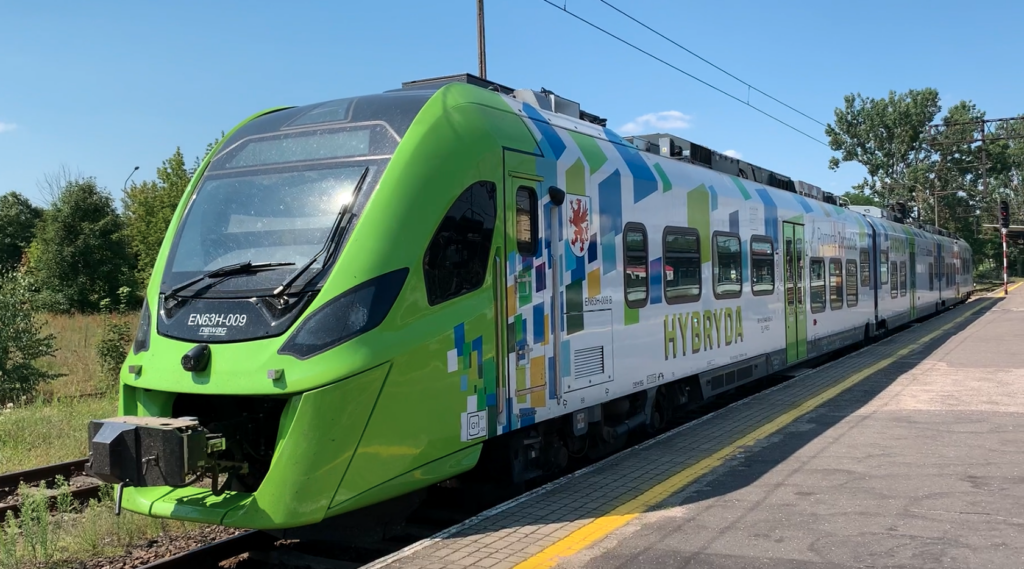
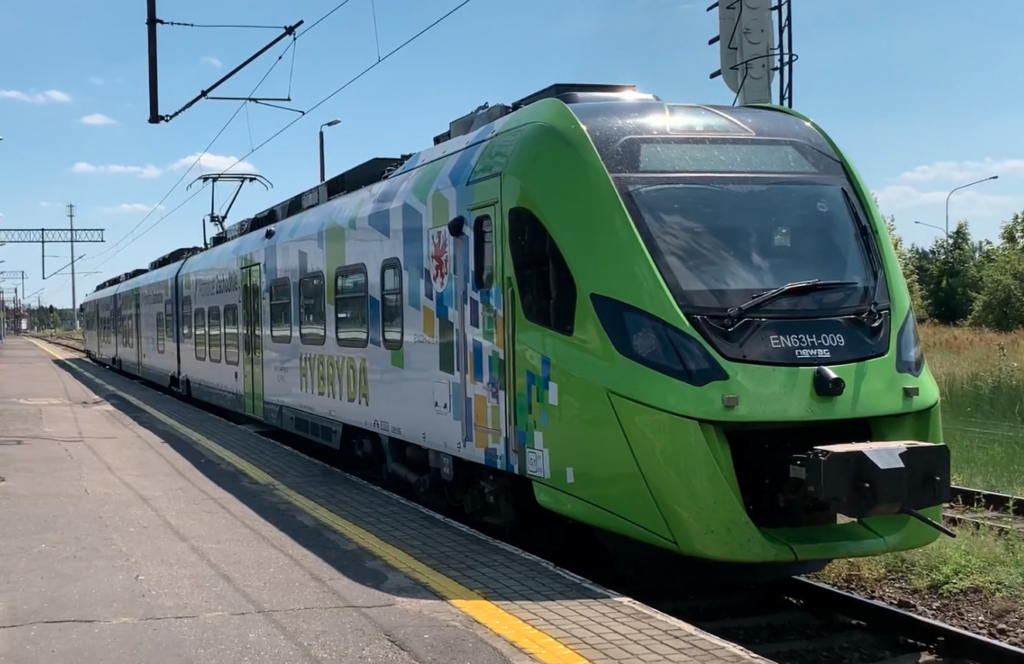
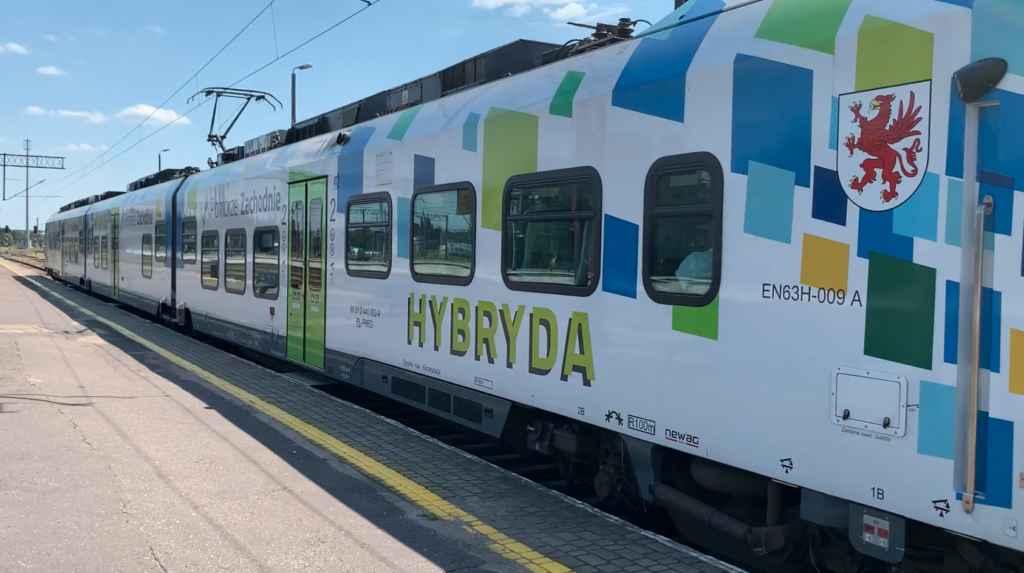
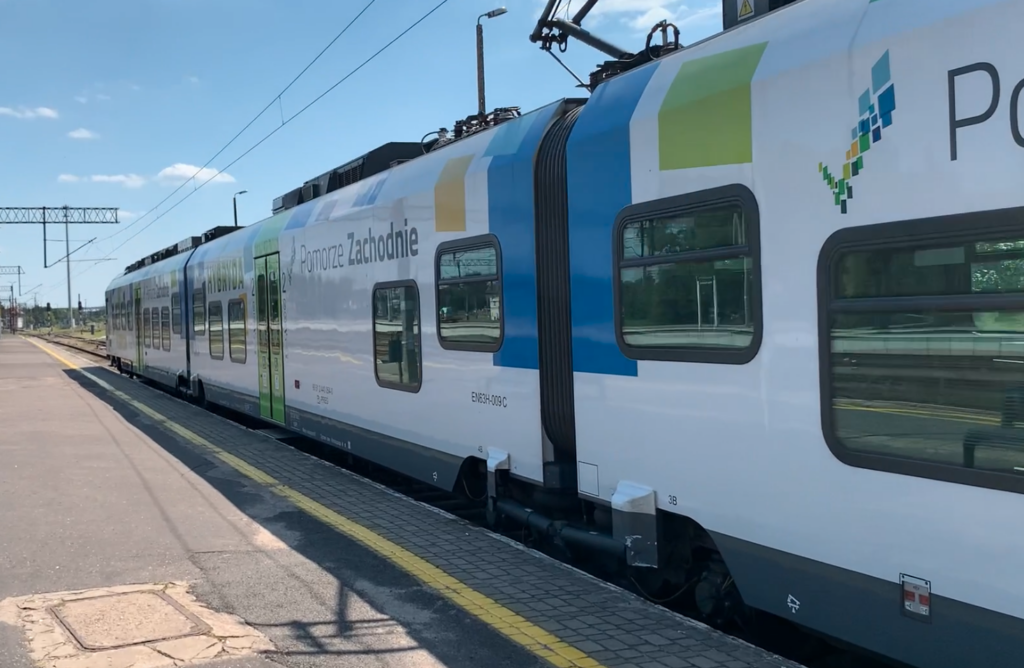
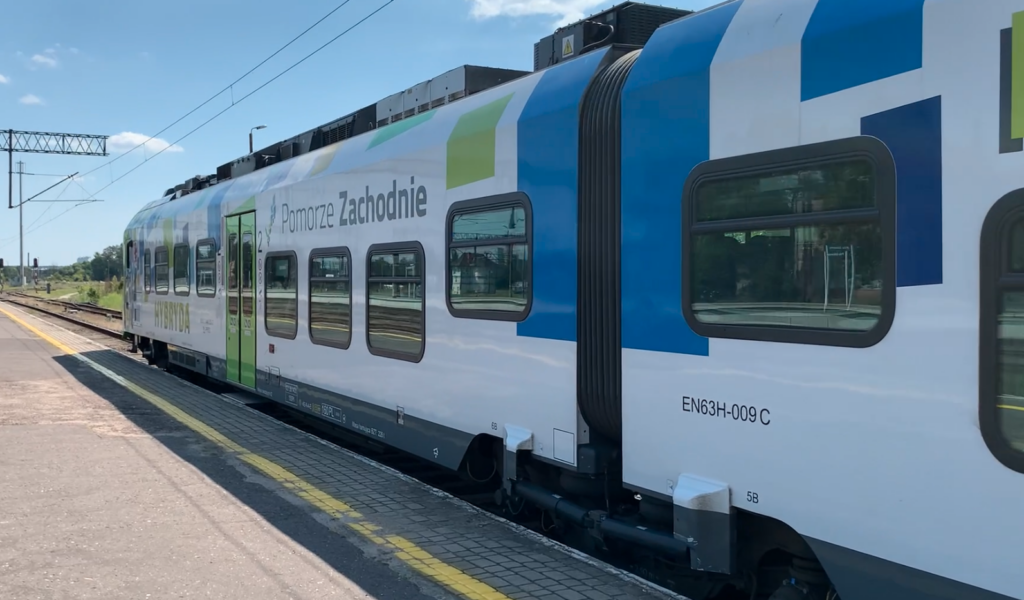
The HZT Impuls 2 series train, type EN63H, factory designation 36WEh, was built in Nowy Sącz in secret and was developed entirely by Polish engineers and technicians. The vehicle is not only innovative, but above all practical and has perfectly fitted into the Polish railway network. As of December 31, 2018, the length of active railway lines in Poland was 19,200 km, including 11,900 km electrified. In the times of the People’s Republic of Poland, it was planned to electrify the entire railway network. However, the national economy, ineptly run by the communists, could not carry out this plan. The HZT Impuls 2 type EN63H (36WEh) vehicle uses innovative technologies that were combined into an efficiently operating system.
In 2019, the vehicle was officially presented during the 13th International TRAKO 2019 Fair in Gdańsk. During this fair, NEWAG S.A. received the main prize in the prestigious competition named after engineer Ernest Malinowski, for products and technical innovations used in the railway industry. The Hybrid Traction Unit Impuls 2 type EN63H (36WEh) was distinguished in the competition.
HZT NEWAG IMPULS 2 type EN63H (36WEh) is the newest and most modern traction unit in the world, which is already used in Poland by several regional railways. This vehicle has stopped the creation of further blank spots on the map of the Polish Railway Network, which excluded a significant part of Polish society from access to this means of transport. The first vehicles of this type were purchased by: the West Pomeranian Voivodeship, the Lower Silesian Voivodeship, the Łódź Voivodeship and the Wielkopolska Voivodeship.
HZT NEWAG IMPULS 2 type 3 EN63H (36WEh) is a three-car train that moves at a speed of 160 km/h under electric traction, and thanks to combustion engines, on routes without wires, moves at a speed of 120 km/h. These are parameters that perfectly fit into Polish tracks. The train takes 330 passengers on board, and importantly, it is adapted for people with limited mobility. Passengers have at their disposal: WIFI, 230 V AC electrical sockets, USB ports, air conditioning, a place to transport a bicycle, a modern passenger information system, window tables, luggage racks, closed toilets.
It can be added that NEWAG also offers bimodal vehicles, i.e. with an additional combustion section. No carrier has ordered such a vehicle yet. Vehicles with hybrid or bimodal drive guarantee a running speed of up to 120 km/h.
New energy storage.
NEWAG is not standing still. In February 2023, it developed the first hybrid traction unit (HZT) in Europe with a supercapacitor storage tank from Medcom. Medcom has developed a supercapacitor energy storage system for the hybrid Impuls 2 traction unit manufactured by NEWAG S.A. The new vehicle was presented in September 2023 at the InnoTrans trade fair and is the first design of this type in the world. The dual-drive vehicle system developed by Medcom consists of traction inverters, which not only control the operation of asynchronous traction motors, but also generate voltage to power on-board systems when driving in diesel mode. Medcom also supplies auxiliary converters, buffer power supplies, TCMS system and low-voltage switchgear for Impuls 2 hybrid trains.
The new HZT EN63H (36WEh) unit presented at the InnoTrans trade fair has been additionally equipped with a supercapacitor storage tank. Thanks to the effective use of electrodynamic braking, implemented by traction inverters during the vehicle’s operation in combustion mode, the supercapacitor storage is charged so that the stored energy can be used in the next cycle. The drive system recovers the kinetic energy of the accelerating vehicle and converts it into electrical energy, which is then stored in the on-board supercapacitor storage. The stored energy is then used during the stop at the station to power the vehicle, as well as to restart it to a speed of about 50 km/h. Thanks to this, the train is able to leave the railway station platform using only clean and free energy.
Mr. Paweł Choduń, Vice President of the Management Board of MEDCOM, explained; – “The expansion of the drive system used so far by us required adding two new elements to the system – a supercapacitor tank and an accompanying DC/DC converter. The energy recovered during braking is first transferred from the traction inverters to the DC/DC converter, which reduces the voltage. Only then does it go to the supercapacitor tank. During the acceleration of the vehicle, the converters increase the voltage, and then the energy is directed to the inverters. Precise system management ensures that the combustion generators increase their power only after the energy from the tank has been exhausted.” According to analyses conducted by NEWAG, on the Goleniów – Kołobrzeg section, the reduction in fuel consumption reached 17% – 22%. Considering the prices of diesel oil and the daily use of the vehicle, this will translate into savings counted in millions of zlotys. An equally important advantage of the modernization is the very quiet operation of the vehicle and the reduction of exhaust fumes during stops at the railway station and during start-up. The control system increases the power of the diesel generators only after covering about 500 meters, which provides increased comfort for passengers waiting on the platforms.
Medcom’s supercapacitor tanks have been used in trams so far. They are used, among others, in PESA JAZZ trams for Warsaw and Gdańsk and in Hyundai Rotem trams for Warsaw.
Data T-T HZT NEWAG IMPULS 2 type EN63H (36WEh):
The train consists of three cars. Axle arrangement Bo’2’2’Bo. Net weight 119,000 kg. Gross weight 120,500 kg. Maximum axle load on the track 183.3 kN. Number of passengers up to 330 people. Length with couplers 59.30 m. Rated power 1,600 kW. Power supply 3 kV DC. Entrance door clearance 1.30 m. Entrance threshold height from railhead 0.62 m. The train can be operated at ambient temperatures from -25 to +40 degrees Celsius. Maximum operating speed; 120 km/h – in diesel mode, 160 km/h – in electric mode. Starting acceleration; ≥0.4m/s² – in diesel mode, ≥1.1 m/s² – in electric mode. Kinematic gauge PN-EN 15273-2:2013. Rail gauge 1435 mm. LED lighting. There is an AED defibrillator on board the train.
PowerPack.
PowerPack series 1800 and 1600 were designed as a compact and flat construction specifically for installation under the floor or on the roof of a traction vehicle. Thanks to this, each PowerPack can be individually configured to meet the requirements of a given rolling stock manufacturer.
The internal combustion drive is provided by MTU series 4000 diesel engines with a power of 390 kW. The 36WEh trains are equipped with two drive units called PowerPack. Each of them consists of a MTU, 6-cylinder, in-line, turbocharged, 390 kW diesel engine. The engine can work with a ZF hydromechanical traction transmission or with a power generator. The latter solution is used in Impuls 2 type 36WEh trains. The engine also has auxiliary devices such as: engine cooler, alternator, air conditioning compressor and air intake and exhaust system. These engines are characterized by; high reliability, ease of maintenance, long periods between repairs and low specific fuel consumption. The transmission is optimized for speeds of up to 120 km/h. The MTU 4000 series diesel engines are manufactured in 6H, 8V, 12V, 16V and 20V cylinder configurations and are suitable for installation in a wide range of locomotives, DMUs and HZTs. They use MTU Common Rail fuel injection. The diesel engines have a good power-to-weight ratio. In the HZT Impuls 2 train, the combustion engine drives a 360 kW generator, which provides a voltage of 2,700 V to 3,050 V.
The MTU PowerPack uses engines; 6H1800 or 12V1600, which are located centrally. The engine shaft speed is transferred either to the gearbox or to the traction generator. On the opposite side of the PowerPack is the cooling system and optional other devices: on-board generator, air compressors, air conditioning, CaPos. The exhaust system is on one side of the combustion engine, and the air intake is on the other side of the engine. The whole rests on a single frame, which can be mounted under the floor of the wagon body or on its roof. The unit can use hydraulic, mechanical or electric gearboxes. Thanks to its compact design, the PowerPack has a Plug & Play configuration, which allows for quick assembly or disassembly and easy access to components. This solution also reduces the weight of the entire unit. MTU PowerPack has electronic control of the most important operating parameters of the unit, which allows for ongoing monitoring of the technical condition of the drive unit. MTU PowerPack meets the EPA Tier 3, 4i and EU Stage IIIB standards. MTU PowerPacks use selective catalytic reduction (SCR) technology, or in Polish, NOx reduction. The drive has a low vibration level and acceptable noise levels.
MTU PowerPack with a power of 2 x 390 kW is installed, for example, in PESA Link and NEWAG 222M Impuls SZT trains. The same drive unit is installed in foreign Bombardier Turbo Star SZTs. On the other hand, 1 to 4 PowerPack 390 kW drive units are installed in Alstom Lint 54 passenger trains; depending on the number of wagons.
MTU also offers Hybrid PowerPack. This is a system additionally equipped with batteries, with a power of 30.6 kWh to 122.4 kWh. This solution has a mechanical transmission and an electric motor or only an electric motor.
Description of HZT NEWAG IMPULS 2 type EN63H (36WEh).
HZT NEWAG IMPULS 2 type 36WEh is a train consisting of three wagons, with the following designations; first wagon “A”, second middle wagon “C”, third end wagon “B”. The train has all the features of EZT Impuls 2 type 36WE. These features include an economical driver’s cabin with the possibility of adding a place for an assistant. The cabin has individual air conditioning and heating. A fridge, kettle, microwave, sink and additional cabinets can be installed. Separate doors leading from the outside have been installed to the engineer’s cabin, both on one and the other side. In the previous EZT Impuls 1 there were no such doors. There is only one door from the passenger part to the cabin. There is no door between the cabin and the engine room, which increases the noise level in the cabin.
Switching from the traction network to diesel traction is simple. We set the direction of travel to Zero. On the systems screen, in the device tab, we give the operating mode window. We lower the pantograph. After a few seconds, we turn on the diesel mode on the screen. When the electronics switch over, we return to the main screen and use the same lever from the pantograph to start the PowerPack. We must remember to turn on the quick switch. It all takes a dozen or so seconds. We do the same in reverse. The pantographs are placed on the middle section of the train.
The floor in the Impuls 2 vehicle is at a height of 0.62 m, and above the bogies 0.76 m. However, in the first and last carriage, where the PowerPack is under the floor, it is higher. Individual carriages can be equipped with a different number of passenger doors. Type 36WEh has one pair of passenger entrance doors in each carriage. This extends the passenger exchange time, but increases the number of seats. The door clearance is 1.30 m. An additional advantage is the reduced number of door automation systems. The interior of the train was designed in consultation with Koleje Wielkopolskie. The entire train is Class 2. The middle carriage is adapted for the travel of disabled people and the transport of bicycles and baby carriages.
In the middle section there is one large toilet in a closed system. The toilet doors are opened manually, because in Impuls 1 trains the automation was failing. The toilet is adapted to serve disabled passengers and is equipped with a baby changing table.
The electric drive motors have a power of 400 or 500 kW. The EN63H (36WEh) vehicle uses 4 x 400 kW electric traction motors. These are three-phase asynchronous motors and are electronically controlled by an inverter. There is one inverter for each bogie. The mechanical transmissions are two-stage.
The vehicle is equipped with automatic Scharfenberg type couplers. A novelty is the covers, which are easy to unlock and move upwards, because they are permanently connected to the coupler. There is no possibility of losing them.
EN63H-009.
The NEWAG EN63H-009 train has the factory number 36WEh-021 and was built in 2022 and was incorporated into the West Pomeranian Plant in Szczecin for the PolRegio carrier in November 2022. The train was painted in white and green with pixels and the inscriptions HYBRYDA.
Written by Karol Placha Hetman
Leave a Reply
You must be logged in to post a comment.